At present, more than 90% of domestic thermal power plants use limestone-gypsum desulfurization technology, which is mature in technology and low in cost. Both of these two processes need to use limestone powder to absorb sulfur dioxide, and the smaller the particle size of limestone powder, the more conducive to the absorption of SO2.
Main Factors Affecting Limestone Desulfurization Efficiency
(1) The quality of limestone
Under normal circumstances, the CaSO4 content in limestone should be higher than 85%, and if the content is too low, it will bring some problems to the operation due to more impurities. The quality of limestone is determined by the content of CaO. The higher the purity of limestone, the better the desulfurization efficiency. But limestone is not necessarily the higher the CaO content, the better. For example, limestone with CaO>54% is marbleized due to its high purity, is not easy to grind, and has strong chemical stability, so it is not suitable for use as a desulfurizer.
(2) Limestone particle size (fineness)
The size of the limestone particle size directly affects the speed of the reaction. When the specific surface area is larger, the reaction speed is faster and the reaction is more sufficient. Therefore, the sieving rate of limestone powder usually required to pass through a 250-mesh sieve or a 325-mesh sieve reaches 90%. That’s it.
(3) Influence of the reactivity of limestone on the performance of the desulfurization system
Limestone with higher activity can achieve higher sulfur dioxide removal efficiency while maintaining the same utilization rate of limestone. Limestone has high reactivity, high utilization rate of limestone, excess CaCO in gypsum, low content, that is, high purity of gypsum.
The working principle of limestone Raymond mill
Limestone Raymond mill is composed of grinding main engine, grading screening, product collection and other components. The main engine adopts an integral casting base structure, and a shock-absorbing foundation can be used. The classification system adopts the structure of mandatory turbine classifier, and the collection system adopts pulse collection.
(1) Working principle of limestone Raymond mill
The material is crushed by the jaw crusher into a particle size that meets the specifications, and is lifted to the storage hopper by the bucket elevator, and then quantitatively sent to the main machine cavity by the feeder for grinding.
The grinding roller device is supported on the plum blossom stand in the main cavity and rotates around the central axis. The grinding roller swings horizontally outward under the action of centrifugal force, so that the grinding roller presses the grinding ring, and the grinding roller rotates around the grinding roller axis at the same time.
The material raised by the rotating blade is thrown between the grinding roller and the grinding ring, and the grinding and grinding effects are achieved by the rolling of the grinding roller.
(2) The working process of the powder separator of limestone Raymond mill
The ground powder is blown by the air flow of the blower to the classifier above the main machine for sieving. If the fineness is too coarse, it will still fall into the main machine for regrinding. The finished product is discharged (the particle size of the finished product can be as high as 0.008 mm).
The purified air flows into the blower through the pipe at the upper end of the cyclone. The air path is circulating. Except for the positive pressure from the blower to the grinding chamber, the air flow in the rest of the pipeline flows under negative pressure, and the indoor sanitary conditions are better.
Limestone Raymond mill technical features
Limestone Raymond mill is a technical update based on the R-type mill. The technical indicators of this product have been greatly improved compared with the R-type mill. It is a new energy-saving mill product. The fineness of the finished product can be adjusted arbitrarily between 38-180μm (80-600 mesh).
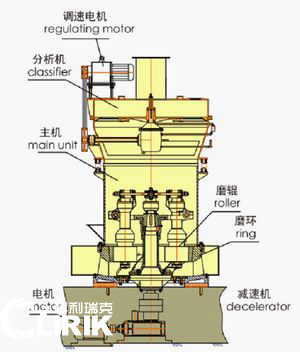
(1) The plum blossom stand and the vertical roller grinding device have advanced and reasonable structure. The machine has very little vibration, low noise, stable mechanical operation and reliable performance.
(2) The processing capacity of materials per unit grinding time is larger and the efficiency is higher. The output has increased by more than 40% year-on-year, and the unit power consumption cost has been saved by more than 30%.
(3) The residual air outlet of the pulverizer is equipped with a pulse dust collector, and its dust collection efficiency reaches 99.9%.
(4) A new sealing structure design is adopted, and the grinding roller device can be filled with grease once every 300-500 hours.
(5) The unique wear-resistant high-chromium alloy material technology is used, which is more suitable for high-frequency and heavy-load collision and rolling conditions, and the service life is extended nearly 3 times that of the industry standard.
HOT PRODUCTS
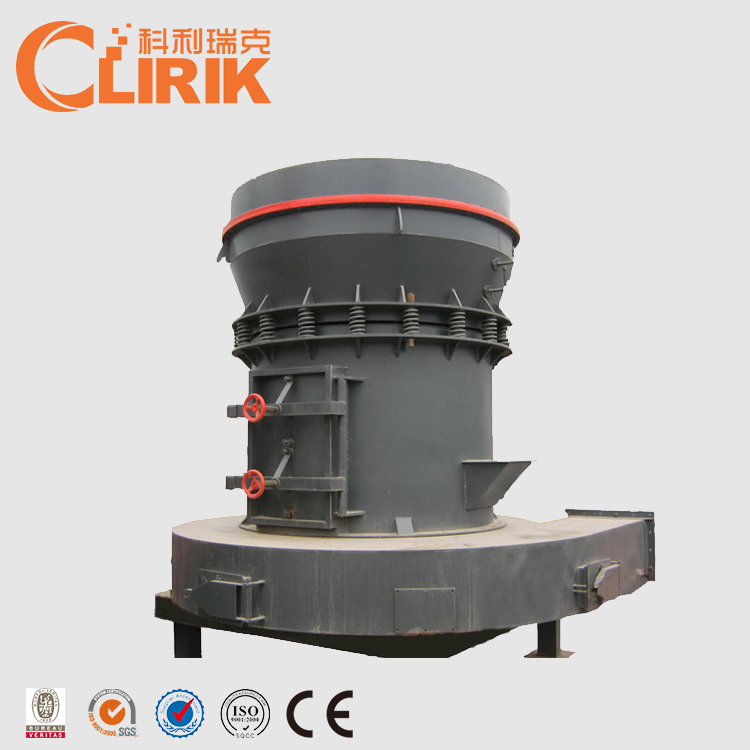
Talc Raymond Mill
Capacity: 1-25 t/h
Max feeding size: 40 mm
Discharge fineness: 50-325 mesh
Range of application: Barite, calcite, potassium feldspar, talc…… [Read More…]
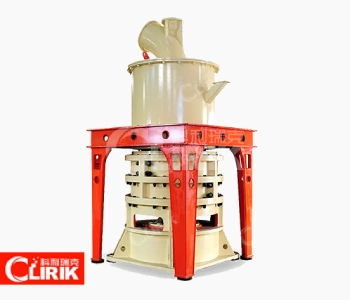
Micro Powder Grinding Mill
Capacity: 0.2-45 t/h
Max feeding size: 20 mm
Discharge fineness: 150-3000 mesh
Range of application: calcium carbonate, kaolin, carbon black, dolomite…… [Read More…]
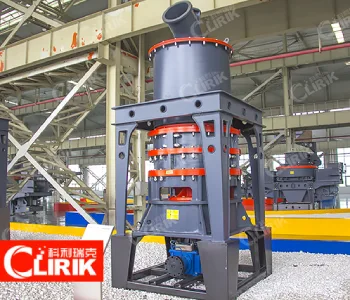
Talc Ultrafine Grinding Mill
Capacity: 0.2-45 t/h
Max feeding size: 20 mm
Discharge fineness: 150-3000 mesh
Processing materials: non-flammable and explosive non-metallic ores with Mohs hardness less than 7…… [Read More…]
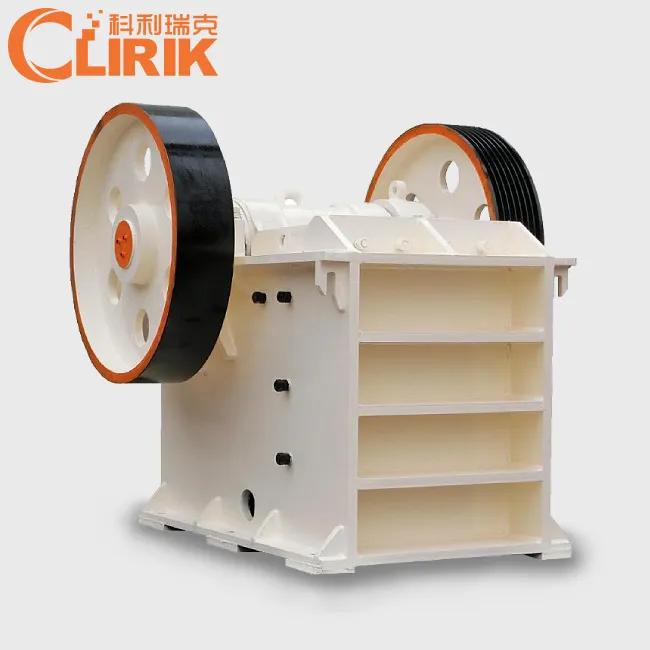
Talc Jaw Crusher
Output Size: 65-160mm
Feed size: 480mm
Capacity: 1-140t/h
Processing materials: Granite, quartz stone, river pebble, calcite, concrete, dolomite…… [Read More…]
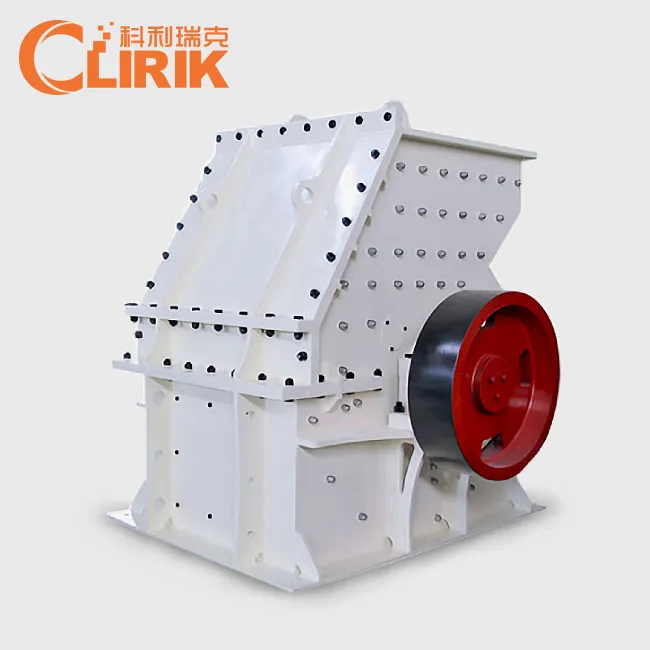
Talc Hammer Mill
Output Size: 5-20 mm
Feed size: <350 mm
Capacity: 5-30 t/h
Application: It is widely used for medium and fine crushing of brittle, medium hardness and soft materials... [Read More…]
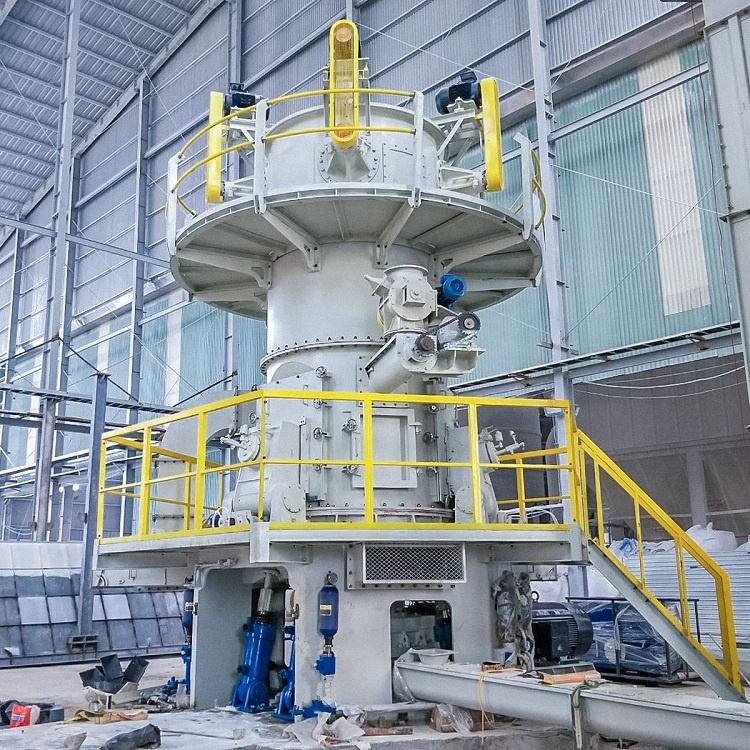
Talc Vertical Mill
Discharge fineness: 150-3000 mesh
Feed size: <15 mm
Output: 1-20 T/H
Product features: It has high grinding efficiency, low energy consumption, uniform particle shape... [Read More…]